С 2020 г. Институт горного дела УрО РАН, сотрудники которого традиционно занимаются разработкой и совершенствованием циклично-поточной технологии для карьеров, принимает участие в создании линейки первых российских дробильно-перегрузочных установок (ДПУ) производительностью 5 000–7 200 тонн в час. Головной разработчик этого оборудования — ПАО «Уралмашзавод», а потребители — горнодобывающие предприятия России и ближнего зарубежья. Сотрудники ИГД УрО РАН обеспечивают научно-технологическую часть проекта — выдают машиностроителям исходные технологические и компоновочные требования на разработку металлоконструкций ДПУ, приспособлений для ее технического обслуживания и ремонта, систем обеспечения рабочей среды и микроклимата (аспирация, пылеподавление, вентиляция и т.п.), а также систем автоматизированного управления. О перспективном проекте рассказал «НУ» заведующий лабораторией транспортных систем карьеров и геотехники ИГД УрО РАН, кандидат технических наук Артем Журавлев.
— Потребность в новых ДПУ возникла в связи с повышением производственной мощности современных горнодобывающих предприятий и неуклонным увеличением глубины открытой разработки месторождений, которая по железорудной отрасли превысила в среднем 300 м. Доставка руды с такой глубины карьерными автосамосвалами требует больших затрат дизельного топлива и иных ресурсов. Рентабельность освоения глубоких месторождений снижается, и часть полезных ископаемых, добыча которых убыточна, приходится оставлять в недрах.
Проблему можно решить благодаря внедрению циклично-поточной технологии транспортирования (ЦПТ). В этом случае доставка руды обходится дешевле и осуществляется комбинированно: в рабочей зоне нижней части карьера — карьерными автосамосвалами до перегрузочного пункта, а далее — более дешевым и высокопроизводительным конвейерным транспортом. В результате на 15–25 % может повыситься производительность и снизиться себестоимость доставки руды из карьера на поверхность. «Сердце» ЦПТ — дробильно-конвейерный комплекс, а его головная часть, определяющая производительность и эффективность рудоподготовки — дробильно-перегрузочная установка (ДПУ).

Перед рабочей группой специалистов Уралмашзавода и ИГД УрО РАН была поставлена непростая задача: создать высокопроизводительные и надежные ДПУ, которые базируются на металлоконструкциях (сейчас в основном используются железобетонные) с единственной головной дробилкой (ранее применялось не менее двух дробилок). По мере необходимости они могут перемещаться с частичной разборкой, должны работать в широком диапазоне температур (от -40 до +45 °С) и в условиях высокой сейсмичности (до 8 баллов) и, конечно же, быть безопасными как для персонала, так и для окружающей среды. При этом времени на разработку и испытание опытных образцов у нас не было — необходимо как можно скорее ввести новые установки в эксплуатацию. В этих непростых условиях команда специалистов решила задачу, определив оптимальные принципы проектирования и разработав методики и алгоритмы моделирования и расчета ДПУ.
Серьезным вызовом стали санкционные ограничения по международной кооперации. Уралмашзавод, а также ряд российских поставщиков комплектующего оборудования с честью выдержали испытание, в короткие сроки самостоятельно разработав и запустив в производство уникальное оборудование: производительный бутобой тяжелого типа с трехсекционной стрелой и мощным гидромолотом; полноповоротный электрогидравлический консольный кран грузоподъемностью 110 т с зоной действия до 22 м (в зарубежных аналогах применяются краны со стрелой в два раза меньше и грузоподъемностью до 80 т); пластинчатый питатель с высокой производительностью 6 000 т/ч; аспирационную установку для пылеудаления из зон, где присутствует персонал. Это стало возможным благодаря напряженной работе и кооперации научных, проектных, машиностроительных и горнодобывающих организаций России.
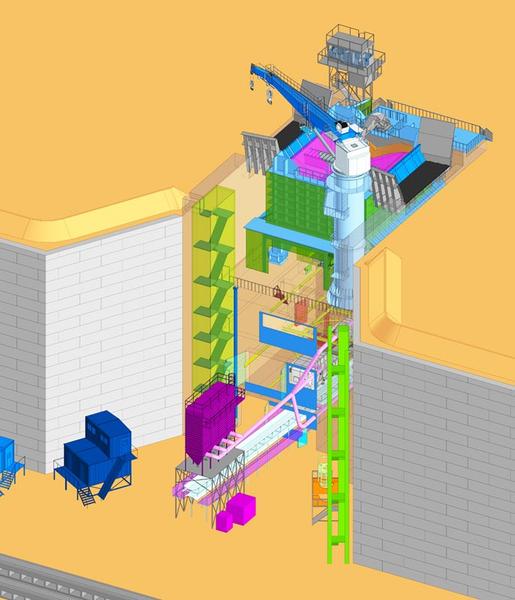
Работа ДПУ автоматизирована, начиная от управления производительностью дробилки и пластинчатых питателей в зависимости от гранулометрического состава, уровней руды в приемном и разгрузочном бункерах, забутовки разгрузочных течек питателей, скорости конвейера и заканчивая автоматическим включением распылителей пылеподавления при разгрузке автосамосвалов в приемный бункер. Операторам дробильно-конвейерного комплекса обеспечены комфортные условия труда с шумо- и виброизоляцией, климатической системой. Вся информация о работе комплекса, в том числе от разветвленной системы видеонаблюдения, выводится на мониторы. За качеством дробленой руды постоянно «следит» система с автоматическим гранулометром и анализатором содержания металла, по сигналам которого регулируются параметры работы дробилки.
Сейчас в производстве на Уралмашзаводе находятся несколько дробильно-перегрузочных установок, уже отгружено более 2 500 тонн металлоконструкций и оборудования ДПУ горнодобывающим предприятиям — Михайловскому ГОКу, Алмалыкскому горно-металлургическому комбинату. Разработка линейки дробильно-перегрузочных установок продолжается. Будут созданы стационарные ДПУ с комбинированными несущими конструкциями, сборно-разборные перемещаемые ДПУ тяжелого типа полностью на несущих металлоконструкциях, а также полностью металлические полумобильные ДПУ, которые перемещаются целиком специальным гусеничным транспортером при частичном демонтаже.
Реализация проекта уже дает не только производственный, но и заметный социальный эффект: создано большое количество новых рабочих мест на Уралмашзаводе, загружаются производственные мощности подрядных организаций по изготовлению металлоконструкций и вспомогательного оборудования как в Уральском регионе, так и за его пределами, обеспечиваются заказами на высокотехнологичное оборудование проектно-инженерные компании и строительно-монтажные организации. После запуска дробильно-конвейерного комплекса появятся новые рабочие места и на горнодобывающих предприятиях. Создание линейки оборудования такого масштаба требует тысяч тонн металла, привлечения сотен специалистов и рабочих, развития научно-инженерных школ, обновления производственных мощностей, что влечет заказы и для смежных отраслей — станкостроения, металлургии и др. А это уже не просто импортозамещение, но опережающее развитие отечественных инновационных технологий и компетенций, обеспечение научно-технологического суверенитета России.
Подготовила
Е. Понизовкина
На рис. слева — модель стационарной дробильно-перегрузочной установки производительностью 6 500 т/ч, встроенной в уступ карьера;
справа — строительство дробильно-перегрузочной установки в карьере